10mm Flat
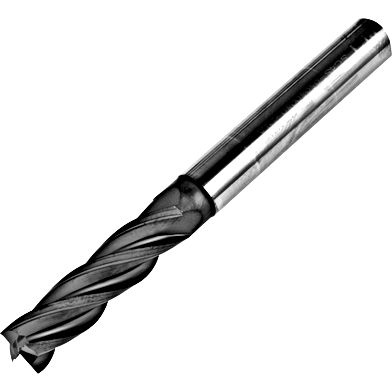
Enhanced Efficiency and Productivity: Boost your efficiency and productivity in graphite machining with our diamond-coated solid carbide end mills . With their exceptional wear resistance and optimized chip evacuation, our end mills enable you to achieve faster machining speeds and higher material removal rates, resulting in increased productivity and cost savings.
Precision Machining Excellence with Diamond-Coated Solid Carbide End Mills: Elevate your graphite machining capabilities with our diamond-coated solid carbide end mills, meticulously engineered for precision and performance. Crafted to meet the unique demands of graphite machining, our end mills deliver unparalleled accuracy and efficiency, ensuring superior results in every application.
Experience precision machining like never before with our diamond-coated solid carbide end mills, meticulously engineered for graphite applications. graphite's abrasive nature and high hardness demand cutting tools of exceptional durability and performance. Our end mills are crafted to meet these exacting standards, delivering unparalleled precision and efficiency in graphite machining.
Built with a robust solid carbide construction, our end mills endure the rigors of graphite machining , ensuring longevity and reliability. The diamond coating enhances the cutting edge's hardness and wear resistance, extending tool life and maintaining consistent performance even in the most challenging conditions.
Our end mills feature a specialized design that optimizes chip evacuation and minimizes tool deflection, resulting in smoother surface finishes and precise dimensional accuracy. Whether shaping intricate contours or performing high-speed machining , our diamond-coated solid carbide end mills consistently deliver superior results with unmatched reliability.
Discover the difference in graphite machining with our diamond-coated solid carbide end mills —the ultimate solution for precision and efficiency.
1. Abrasion Resistance: Diamond is known for its exceptional hardness and resistance to wear, making it an ideal coating for end mills used in graphite machining. This hardness ensures a longer tool life and consistent performance.
2. Heat Resistance: diamond-coated end mills can withstand high temperatures generated during machining processes, reducing the risk of tool failure and ensuring reliable performance.
3. Smooth Cutting Action: diamond-coated end mills provide a smooth cutting action, minimizing graphite dust generation and reducing the risk of tool clogging.
4. Improved Surface Finish: The smooth cutting action of diamond-coated end mills also leads to better surface finishes on machined graphite components.
5. Cost-Effective: Although diamond-coated end mills may have a higher initial cost, their longer tool life and improved performance can result in cost savings over time.
To maximize the benefits of diamond-coated solid carbide end mills for graphite machining , consider the following actionable steps:
1. Choose the right Diamond coating: Select a diamond coating that matches your specific machining requirements, such as coating thickness, uniformity, and bonding strength.
2. Proper tool selection: Select the appropriate end mill geometry, such as flute count, helix angle, and corner radius, based on your specific machining application.
3. Optimal cutting parameters: Follow the manufacturer's recommended cutting parameters, such as spindle speed, feed rate, and depth of cut, to ensure optimal tool performance and longevity.
4. Coolant selection: Use coolant or lubricant specifically designed for graphite machining , as it can help reduce tool wear and improve tool life.
5. Regular tool maintenance: Inspect the Diamond-coated end mills regularly for signs of wear or damage. Replace them when necessary to maintain consistent performance and prevent tool failure.
6. Proper storage: Store the Diamond-coated end mills in a clean, dry place to prevent damage and prolong their lifespan.
7. Operator training: Ensure that operators are properly trained in the safe and efficient use of Diamond-coated end mills , as well as understanding the importance of following safety guidelines and proper maintenance procedures.
Item | R | d | D | ℓ | L |
HNS7520210050 | r1.0 | 2 | 4 | 10 | 50 |
HNS7520315050 | r1.5 | 3 | 4 | 12 | 50 |
HNS7520420060 | r2.0 | 4 | 4 | 15 | 60 |
HNS7520525060 | r2.5 | 5 | 5 | 20 | 60 |
HNS7520630075 | r3.0 | 6 | 6 | 80 | 75 |
HNS7520840080 | r4.0 | 8 | 8 | 35 | 80 |
HNS7521050090 | r5.0 | 10 | 10 | 40 | 90 |
HNS7521260100 | r6.0 | 12 | 12 | 45 | 100 |
HNS7320210100 | r1.0 | 2 | 4 | 10 | 100 |
HNS7320315100 | r1.5 | 3 | 4 | 12 | 100 |
HNS7320420100 | r2.0 | 4 | 4 | 15 | 100 |
HNS7320525100 | r2.5 | 5 | 5 | 20 | 150 |
HNS7320630100 | r3.0 | 6 | 6 | 80 | 150 |
HNS7320840150 | r4.0 | 8 | 8 | 35 | 150 |
HNS7321050150 | r5.0 | 10 | 10 | 40 | 150 |
HNS7321260150 | r6.0 | 12 | 12 | 45 | 150 |
Item | d | D | ℓ | L | |
HNS75402060 | 2 | 4 | 10 | 60 | |
HNS75403060 | 3 | 4 | 12 | 60 | |
HNS75404075 | 4 | 4 | 15 | 75 | |
HNS75405075 | 5 | 5 | 20 | 75 | |
HNS75406080 | 6 | 6 | 80 | 80 | |
HNS75408080 | 8 | 8 | 35 | 80 | |
HNS75410100 | 10 | 10 | 40 | 100 | |
HNS75412110 | 12 | 12 | 45 | 100 |
How to Buy
Request an Equipment Quote
Ready to buy stuff from Flexible,Request a quote now.
Buy
Browse Parts and equpments on our store